Mark Zuckerberg Reveals Meta Superintelligence Labs, Names Who He Poached From OpenAI, Google, AnthropicIn a leaked internal memo, Zuckerberg wrote that former Scale AI CEO Alexandr Wang would lead the new team.Meta CEO Mark Zuckerberg, 41, is reshaping the company's AI efforts to focus on superintelligence, or AI that surpasses human intelligence.
In a memo to employees on Monday, released in full by CNBC, Zuckerberg announced that a new group called Meta Superintelligence Labs, or MSL, will house Meta's AI initiatives going forward. Alexandr Wang, the 28-year-old former CEO of AI training data startup Scale AI, will lead the group and assume the newly created role of Meta's Chief AI Officer (Meta has a separate Chief AI Scientist, Yann LeCun).
In the memo, Zuckerberg called Wang the "most impressive founder of his generation" and said that former GitHub CEO Nat Friedman would "partner" with Wang to lead the MSL team. The new unit will encompass Meta's existing teams that focus on developing AI models and AI products. It will also include Meta's fundamental AI research (FAIR) team.
"As the pace of AI progress accelerates, developing superintelligence is coming into sight," Zuckerberg wrote in the memo. "I believe this will be the beginning of a new era for humanity, and I am fully committed to doing what it takes for Meta to lead the way."
Meta previously announced a $14.3 billion investment in Scale AI earlier this month in exchange for a 49% stake and fresh talent from the startup, including Wang.
Alexandr Wang. Photographer: David Paul Morris/Bloomberg via Getty Images
Zuckerberg also wrote that Meta would bring on 11 new hires for MSL, including researchers from competitors like OpenAI, Google, and Anthropic. The new team includes former Google DeepMind researchers Jack Rae and Pei Sun, OpenAI researchers Trapit Bansal and Hongyu Ren, and Anthropic software engineer Joel Pobar.
In the memo, Zuckerberg said that Meta's vision for AI was "personal superintelligence for everyone" and that the company was going to start working on its next generation of AI models to debut "in the next year or so."
Meta CEO Mark Zuckerberg. Photographer: David Paul Morris/Bloomberg via Getty Images
Meta has a broad reach: Zuckerberg disclosed in May that the company's AI is used by more than one billion monthly active users across its apps, including Facebook, Instagram, and WhatsApp.
The company is also investing heavily in AI, with plans to spend $60 billion to $65 billion this year alone on AI infrastructure.
Meta also isn't afraid to spend heavily on AI talent. OpenAI CEO Sam Altman stated earlier this month that Meta was offering "$100 million signing bonuses" and "more than that" in compensation to many OpenAI researchers to poach talent.
Meta's CTO, Andrew Bosworth, refuted the claims last week in a leaked all-hands meeting, saying that Altman was "being dishonest" about the signing bonuses and compensation.
"Look, you guys, the market's hot," Bosworth said at the meeting. "It's not that hot."
Meta is the sixth most valuable company in the world, at press time, with a market cap of over $1.8 trillion.
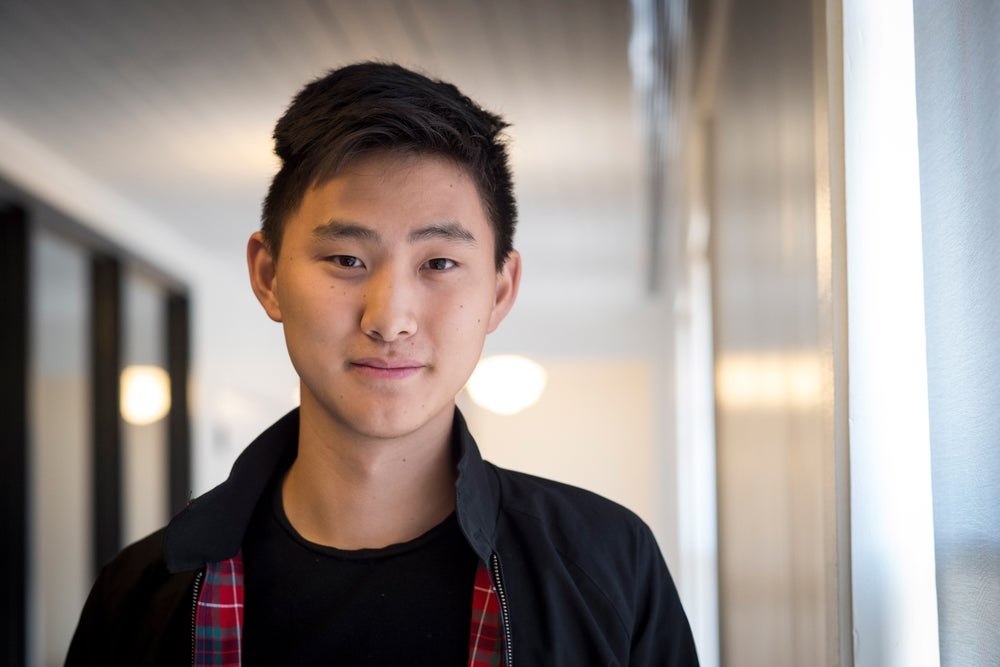
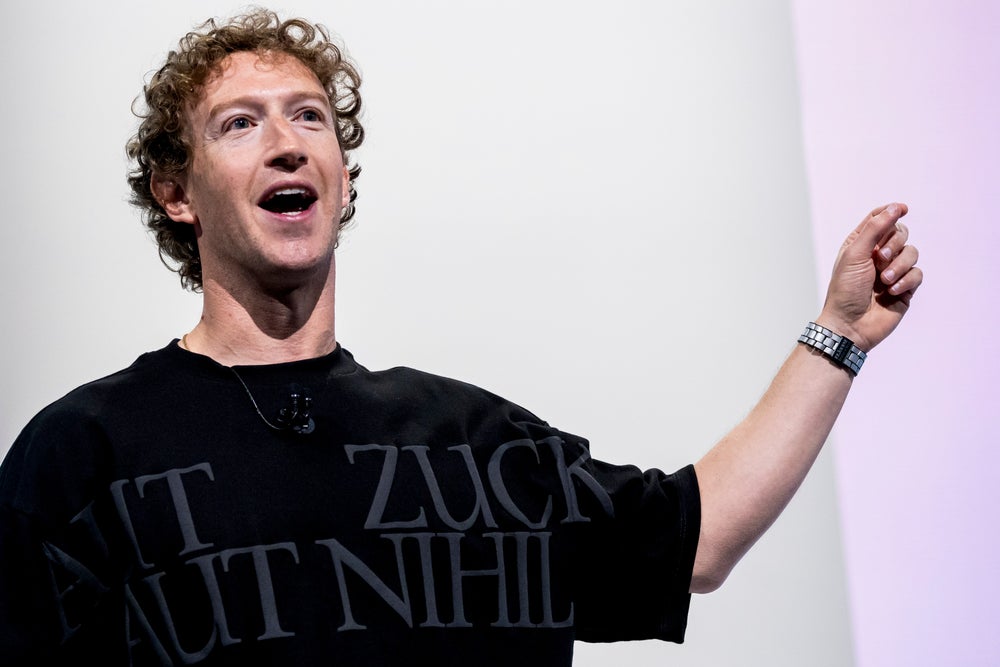